Types of valves
The variation in valve types is huge: from ball valves to butterfly valves and from gate valves to globe valves. Each valve type has its own functionality, advantages and disadvantages. When do you apply which valve? You can read all about it below.
Engineering Team
7 min read
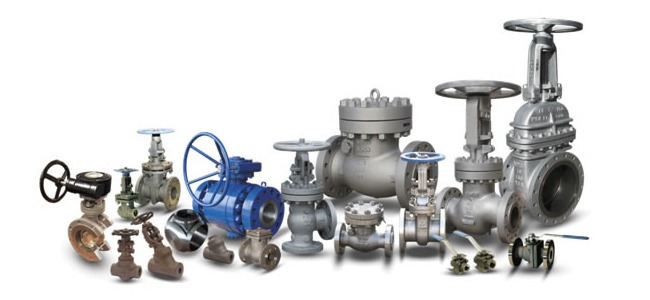
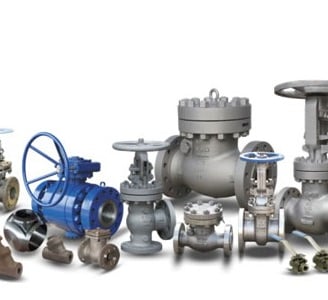
Types of Valves
when to apply which one?
First of all, an important side note must be admitted here. In all honesty, there is no clear and set instruction, roadmap or guide that simply tells you which type of valve should be used when within each industry and application. The differences between various applications are simply too great to be able to assign universal solutions. Within this restriction, however, we can indicate the global comparisons and contrasts between the distinct general types. While doing so, we can indicate the most common applications in which these types are used. As long as the below information is taken with this understanding in mind, a basic understanding of which valve is generally used when can be gained.
Below are the most common types of valves and a description of when they are commonly used, and when they are no
The butterfly valve
We generally start with the butterfly valve because it is the most common valve in the industry. The reason is simple: in its standard version, the butterfly valve is often the cheapest and simplest valve there is.
In addition, the butterfly valve is available in very large dimensions. A butterfly valve is a valve that shuts off all or part of the flow of a liquid or gas with a disc that rotates around its axis. Rotation through an angle of 90° moves the butterfly valve from open position to closed position or vice versa. Because the design is quite simple, relatively few parts are required and the complexity of the components used is quite low. If we add to this the fact that low amounts of material are required to design butterfly valves, we can draw the conclusion that the butterfly valve is a low-cost, lightweight and compact solution.
The simplest version is the centric version with a rubber or PTFE sealing. As temperature range and pressure range requirements become more stringent, a double-, triple-, or even quadruple eccentric version can be used. The disadvantage of a butterfly valve is the butterfly or disc itself, which forms an obstruction for the medium. This can cause unwanted pressure losses and accumulation of the medium if it contains solids. For these reasons, one may opt for a different valve.
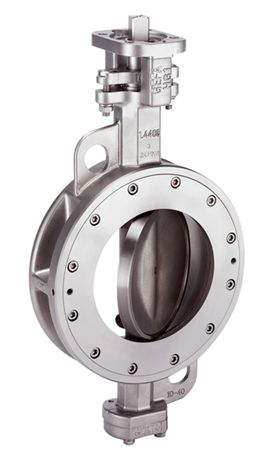
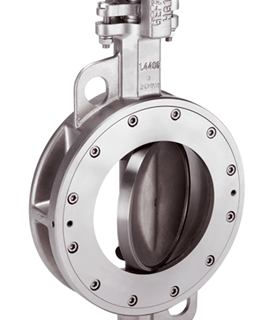
The ball valve
Right after the butterfly valve we see the ball valve as the second-most common valve in the industry. The reason for this is similar to that of the butterfly valve: a ball valve is a compact, lightweight and relatively inexpensive solution to shut off flow. A ball valve is a valve that shuts off all or part of the flow of a liquid or gas with a ball that rotates arround its axis. By rotating the ball 90°, the valve goes from open position to closed position or vice versa. While doing this, the ball valve offers one major advantage over a butterfly valve: it has little to no obstruction in the flow, which means that it causes less pressure loss than a butterfly valve and reduces the ability of the medium to accumulate. In case a full bore version is chosen instead of a reduced bore, this pressure loss figure is reduced even further. Ball valves are available in various designs and materials and can be equipped with a wide variety of sealing technologies. This makes them applicable for a large temperature range and pressure range.
However, the ball valve has two major drawbacks: due to its design, the total cost of the ball valve increases significantly as the pipe diameter increases. The costs accumulate particularly from size DN150 onwards. In addition, the most commonly used design - the floating ball design - has a number of dead spaces surrounding the ball in which the medium can accumulate. Selecting a trunnion design prevents this, but this results in relatively high purchasing costs.
In short: for larger pipe diameters and for systems in which dead spaces are undesirable, the ball valve is less suitable and another valve may be preferred.
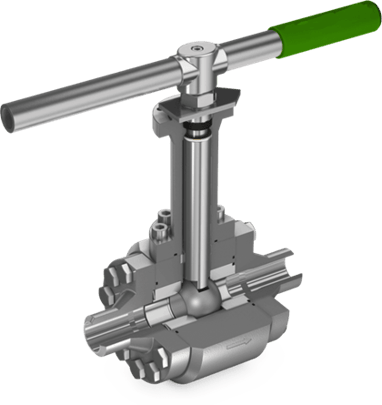
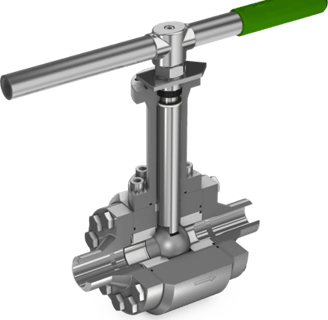
The gate valve
Although butterfly valves and ball valves are the most widely used valves in industry, they share one disadvantage and bottleneck. Whenever the medium contains solid particles such as sludge, fibres, pulp, powders, etc., there is a danger of accumulation. In this case, both the ball valve and butterfly valve may jam and fail. The gate valve provides a solution for this. In a gate valve, a gate is pushed into the path of the flowing medium in vertical movement using a spindle. The valve opens fully and closes off the pipe completely. With a knife-edge version, the valve plate will be able to cut through remaining parts of the medium to ensure complete tightness. Gate valves are available in various versions and designs depending on the exact requirements and circumstances.
A shared advantage of all gate valves is their ability to properly seal a viscous, dirty and/or slurry-forming medium. A shared disadvantage of all gate valves is the fact that they are relatively large and heavy and thus are relatively expensive compared to other valve types. Also, due to the vertical movement required, the operating time of a gate valve is often considerable. The gate valve is generally a more expensive solution than butterfly valves and ball valves and is therefore used for specific applications where the above valve types are insufficient.
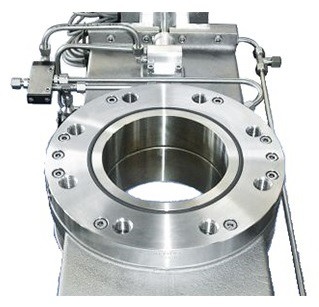
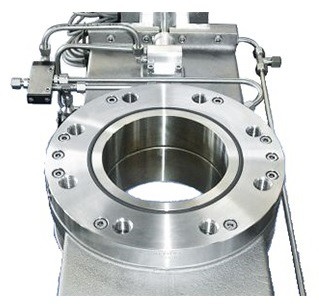
The globe valve
The globe valve is similar to the gate valve in terms of linear operation. Both valve types close the pipe by means of a spindle or stem, using a linear movement (multi-turn). This in contrast to the ball valve and butterfly valve, which utilize a rotary movement (quarter-turn). In a globe valve, a so-called globe is pushed down into a specifically designed seat by means of a spindle or stem. The design of the globe can be adapted depending on the exact application but in almost all cases concerns a flat disc in the shape of a flat cone.
Although its operation is similar to a gate valve; its primary function is not. Due to the shape of the cone, a globe valve is able to shut off very precisely and thus achieve a fairly linear flow. This makes globe valves ideal for the function of control and modulation. Depending on the materials used, globe valves are also suitable for very high pressures. Globe valves are therefore often used as control valves and/or high-pressure valves. The advantage clearly is the precision of closure and the linearity of the pressure loss.
A disadvantage of a globe valve can be that a full opening is not created (no full-bore) and that the design is rather expensive compared to a simple gate valve, butterfly valve or ball valve. A very compact version of the globe in the form of a needle / narrow cone is also called a needle valve. The needle valve is mostly used for very small diameters or for very precise regulation. For large diameters above DN300, both the globe valve and the needle valve are unsuitable due to the high costs involved.
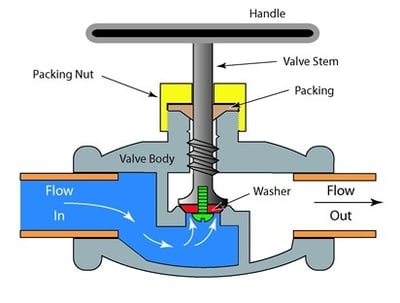
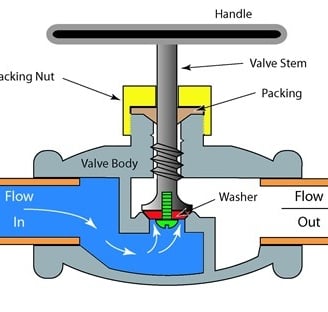
The diaphragm valve
A diaphragm valve consists of a steel or stainless steel body which is included with a rubber diaphragm that is compressed by a spindle in a linear movement. While compressing the diaphragm, the valve shuts off. This relatively simple design causes that few rotating or moving parts are required which implies there are a low amount of wear parts . In addition, diaphragm valves generally achieve an un-interrupted, full bore passage minimizing pressure loss. The main application for diaphragm valves are processes with highly abrasive media such as the cement industry and mining.
The diaphragm, which is often made of an elastomer, is relatively insensitive to wear and tear and can be easily replaced. The disadvantage is that these valves can only be used for shutoff applications and that regulation is impossible. In addition, diaphragm valves are unsuitable for high temperatures and pressures, vacuum processes and gases. Finally, diaphragm valves become significantly more expensive once the dimensions become larger.
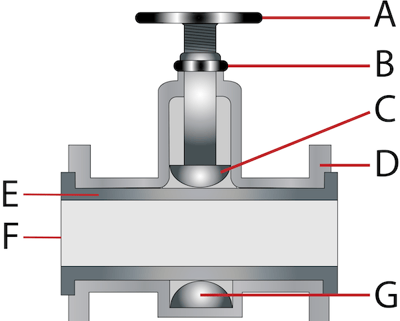
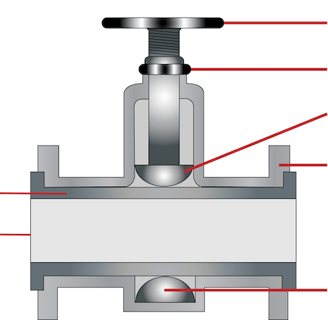
The non-return valve,
or check valve
The check valve is a general term for all valves that do not open and close by means of a manual or automatic actuator but which are opened and closed by the medium itself. There are various designs of check valves: swing check valves, dual plate check valves, disco check valves, tilting disc check valves, ball check valves, etc. All non-return valves share the principle that the shutting element- in whatever version - is pushed open whenever the medium enters the valve upstream.
When the medium is completely through the valve and there is no more upstream pressure, the valve closes due to a lack of pressure. The same happens whenever the medium flows back towards the valve. As a result, non-return valves are mostly used as safety devices for protecting critical components such as pumps. This function is also the main advantage of the non-return valve: it protects critical components automatically without the need for any action. However, this trait can also be a disadvantage: in most cases, a non-return valve cannot be operated, so an additional valve that is required to control the process.
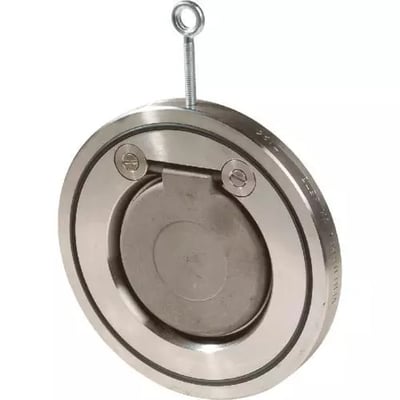
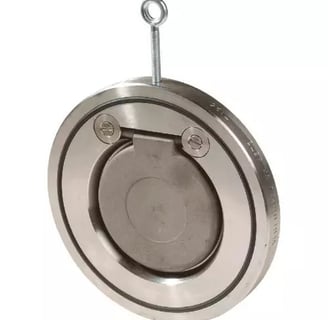